Fatigue crack growth testing is a critical process for understanding how materials deteriorate under repeated or cyclic loading. When materials experience fluctuating stresses over time, tiny cracks can begin to form at vulnerable points whether due to inherent weaknesses, environmental exposure, or operational demands. These small cracks might initially seem inconsequential, but they steadily grow as the material endures more cycles of loading, eventually compromising the material’s integrity and leading to failure.
This testing method focuses on quantifying the rate of crack growth under controlled conditions, providing a deeper understanding of how long a material can sustain operational loads before it reaches a critical failure point. By varying parameters like load intensity, frequency, and environmental conditions, fatigue crack growth tests simulate real-world scenarios, closely replicating the conditions materials face in the field. Specimens for these tests are often customized to reflect specific applications, ensuring relevant and actionable results.
Data from fatigue crack growth testing is invaluable for product developers and engineers, as it helps predict a material’s lifespan under specified conditions. This predictive power allows for proactive maintenance schedules, repair guidelines, and well-informed decisions on replacement intervals. Ultimately, this testing contributes to creating safer, more reliable products, minimizing unexpected failures, and optimizing cost by planning maintenance and replacements with accuracy.
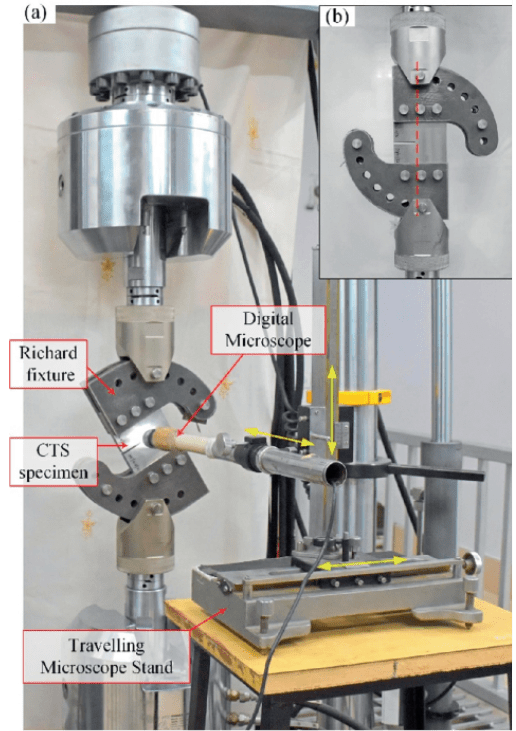
Fatigue crack growth testing describes the rate a pre-existing crack will grow under time-varying crack tip driving force. Often described also as crack propagation or da/dN testing, fatigue crack growth tests at LTI using both compliance and DC potential drop-crack length measurement techniques. Material tests are then analyzed with either K or load control. Advanced customised test methodologies are also available to characterise threshold and complete Region I, Region II, referred to as the “Paris” regime, and Region III crack growth.
All standard geometries of test specimens are machinable. Compact tension (C(T)) and middle tension (M(T)) specimen configurations over several sizes support fatigue crack growth analysis. The M(T) specimen is intended for sheet materials, while the C(T) permits various different material forms to be tested, including sheet, plate, bar, and forgings. LTI may also prepare and test surface-flaw and SEN(T) specimens. Wire EDM creates starter notches, as in this case.
Laboratory Testing Inc. offers fatigue crack growth testing by a highly qualified team at our greater Philadelphia laboratory. These tests comply with ASTM E647 and ASTM E2899. In addition, variable-amplitude fatigue crack growth (spectrum testing), dwell testing, and even custom customer waveforms are available. The Adjusted Compliance Ratio, compression pre-cracking, K-control, and constant Kmax testing are just a few of the options possible.
Capabilities
Specifications: ASTM E647, ASTM E2899
Parameters: Constant, increasing /decreasing ΔK, constant Kmax
Max Loading: 100,000 lbs
Temperature: -323°F to 1800°F
Specimen Type: C(T) – compact tension, M(T) – middle tension, SEN(T) – single edge notch tension, Kb Bar (surface flaw and corner crack)
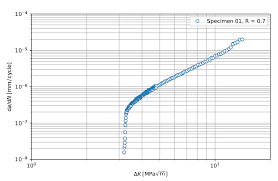
Group Your Material Testing at LTI
Fatigue crack growth testing observes how cracks develop under various loading and environmental conditions to simulate the service life within a compact schedule. Fracture and fatigue testing is not our only service; however, with a full slate of equipment and field experts across various mechanical domains. We can handle all your material testing in a single location. Our customer portal delivers concise reporting so you can easily track results for project approvals and maintain on-schedule production.
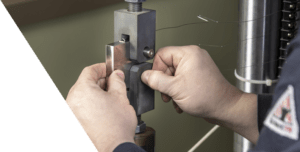