WHAT IS A FATIGUE TEST?
It is a controlled and systematic procedure for evaluating the inherent ability of a material to withstand cyclic loading conditions. Such repeated stresses, often involving tension, compression, bending, torsion, or combinations of those, may cause damage to the material or failure in the case of the latter, even though loads applied are less than the ultimate strength of the material.
The output data of the fatigue test do contain very important information on the durability and safety of materials used in critical applications, from aerospace components to parts for automobiles and in structural engineering.
What is the phenomenon of fatigue in materials?
This is a mechanical degradation phenomenon characterized by progressive, localised and permanent structural changes that occur in material under fluctuating stresses and strains. The phenomenon is often associated with the behavior of materials subjected to cyclic loading, bringing about a critical point at which the material may develop cracks and eventually fail, even though the applied loads may remain below the ultimate strength of the material.
The nature of plastic deformation brings about deformations that may take on a micro-scale when the materials are in a state of fatigue. Hence, accumulation of these localised deformations under continued stress leads to macroscopic damage and eventually to failure in fracturing the material or component.
Fatigue Test: How to do it?
Fatigue testing involves loading a specimen into the fatigue testing machine, applying a predetermined stress, and then unloading it to zero load in the opposite direction until the end of the test. The time for which the test is performed may be predefined by cycles or to the failure of the specimen, as specified by the test parameters.
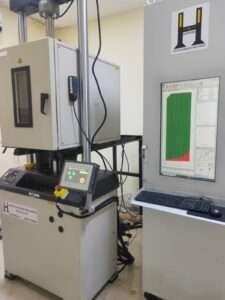
Fatigue testing is carried out for several purposes.
The principal purpose of a fatigue test is typically to determine the service life expected in a material under cyclic loading. Besides this, fatigue strength and resistance against cracking are other significant parameters. Fatigue life refers to the cumulative number of cycles a material is capable of resisting under one specific load regime. A fatigue test is also useful to determine the maximum load a specimen can endure for a given number of cycles. All these attributes are of immense importance in industries where materials are subject to fluctuating, rather than constant, forces.
Fatigue of understanding and testing has become very important from car chassis in formula 1 to dental implants while designing the components subjected to cyclic loads. Fatigue tests have helped make predictions regarding the service life and assess the durability of the component through related levels of applied stress, providing assurance about the reliability of materials used across applications.
Materials under various application types.
There are several kinds of fatigue test High cycle fatigue test: Standard fatigue test carried out at frequencies ranging approximately between 1 and 5000 Hz.
HCF (DIN 50100) High cycle fatigue test: Standard fatigue test carried out at frequencies ranging approximately between 1 and 5000 Hz.
Bending fatigue test on rotating bars, DIN 50113.
Tensile-compression fatigue tests. Testing strength (fatigue strength) against cyclic stresses using tension, unloading and compression.
Giga-cycle fatigue test: A fatigue test in which at least 1 × 10^9 cycles or more are applied in a very short time with ultrasonic vibrations, etc.
Fatigue crack propagation test machine: A machine meant to study the rate of crack propagation under cyclic stresses.
ASTM D3479 – Tension-Tension Fatigue of Polymer Matrix Composite Materials
ASTM D7774 – Flexural Fatigue Test Equipment for Plastic Materials
ASTM E2207 – Equipment for Testing Axial-Torsion Fatigue in Thin-Walled Tubular Materials
ASTM E2368 – Thermomechanical Fatigue Test Equipment
ASTM E466 – Controlled-Load, Constant-Amplitude Fatigue Testing of Metals
ASTM E467 – Constant Force Axial Fatigue Test System – Testing Machines
ASTM E606 – Strain-Controlled Fatigue Testing at High and Low Cycles
DIN EN 6072 – Aerospace Series – Metallic Materials – Test Methods – Constant Amplitude Fatigue Testing
DIN 50100 – Controlled Load Fatigue Tests – Performance and Evaluation of Cyclic Tests with Constant Load Amplitude on Metal Specimens and Components
ISO 1099 – Metallic Materials – Fatigue Tests – Controlled Axial Force Method
ISO 7206 – Testing of Hip Implants
ISO 14801 – Equipment for Fatigue Testing of Dental Implants
ISO 15024: Testing Machines – Interlaminar Fracture toughness Testing of Plastic Composite Materials
ISO 22675: Facilities for Fatigue Testing of Protective Ankle and Foot Devices
Fatigue testing is carried out for several purposes.
The principal purpose of a fatigue test is typically to determine the service life expected in a material under cyclic loading. Besides this, fatigue strength and resistance against cracking are other significant parameters. Fatigue life refers to the cumulative number of cycles a material is capable of resisting under one specific load regime. A fatigue test is also useful to determine the maximum load a specimen can endure for a given number of cycles. All these attributes are of immense importance in industries where materials are subject to fluctuating, rather than constant, forces.
Fatigue of understanding and testing has become very important from car chassis in formula 1 to dental implants while designing the components subjected to cyclic loads. Fatigue tests have helped make predictions regarding the service life and assess the durability of the component through related levels of applied stress, providing assurance about the reliability of materials used across applications.
Materials under various application types.
- There are several kinds of fatigue test High cycle fatigue test: Standard fatigue test carried out at frequencies ranging approximately between 1 and 5000 Hz.
HCF (DIN 50100) High cycle fatigue test: Standard fatigue test carried out at frequencies ranging approximately between 1 and 5000 Hz.
Bending fatigue test on rotating bars, DIN 50113.
Tensile-compression fatigue tests. Testing strength (fatigue strength) against cyclic stresses using tension, unloading and compression.
Giga-cycle fatigue test: A fatigue test in which at least 1 × 10^9 cycles or more are applied in a very short time with ultrasonic vibrations, etc.
Fatigue crack propagation test machine: A machine meant to study the rate of crack propagation under cyclic stresses.
Most widely used fatigue tests
ASTM D3479 – Tension-Tension Fatigue of Polymer Matrix Composite Materials
ASTM D7774 – Flexural Fatigue Test Equipment for Plastic Materials
ASTM E2207 – Equipment for Testing Axial-Torsion Fatigue in Thin-Walled Tubular Materials
ASTM E2368 – Thermomechanical Fatigue Test Equipment
ASTM E466 – Controlled-Load, Constant-Amplitude Fatigue Testing of Metals
ASTM E467 – Constant Force Axial Fatigue Test System – Testing Machines
ASTM E606 – Strain-Controlled Fatigue Testing at High and Low Cycles
DIN EN 6072 – Aerospace Series – Metallic Materials – Test Methods – Constant Amplitude Fatigue Testing
DIN 50100 – Controlled Load Fatigue Tests – Performance and Evaluation of Cyclic Tests with Constant Load Amplitude on Metal Specimens and Components
ISO 1099 – Metallic Materials – Fatigue Tests – Controlled Axial Force Method
ISO 7206 – Testing of Hip Implants
ISO 14801 – Equipment for Fatigue Testing of Dental Implants
ISO 15024: Testing Machines – Interlaminar Fracture toughness Testing of Plastic Composite Materials
ISO 22675: Facilities for Fatigue Testing of Protective Ankle and Foot Devices